4flow supports strategy development, service provider selection, and implementation
With nine manufacturing sites in Europe, North America and Asia and regional offices and locations in over 85 countries, ENGEL AUSTRIA GmbH is the global leader in injection molding machinery manufacturing. With its worldwide network of service technicians, the ENGEL customer service division ensures that customers’ machines are readily supplied with replacement parts for repair and maintenance. With availability and delivery performance requirements increasing at an elevated rate, the need for expanding ENGEL’s spare part capacities was growing ever more urgent – especially in order to ensure that future customer demand could be met efficiently.
Up until recently, ENGEL had been providing its customers with spare parts using its Austrian manufacturing plants in Schwertberg, St. Valentin, and Dietach, which were already very near peak capacity. The creation of spare parts hubs in the US and Thailand shortened delivery times, but did not solve the issue of bottlenecks in production. Short-notice orders for spare parts entailed significant additional effort, and available floor space at the existing manufacturing sites was limited. For these reasons, a long-term solution with the potential to accommodate future growth was needed.
New strategy for spare parts logistics
4flow collaborated with ENGEL to conduct a strategy study focused on a make-or-buy decision for ENGEL’s spare parts business. Once the requirements of the future solution were derived from the study, 4flow and ENGEL developed a corresponding strategy for future-proofing ENGEL’S spare parts operations. Three options were on the table:
- Expansion of the spare parts warehouses at the existing ENGEL sites
- Construction of a new site, to be operated by ENGEL
- Establishment of an external spare parts warehouse, to be operated by a partner company
With the aid of the strategy study and 4flow’s expertise in aftersales, ENGEL elected to solve the issue by utilizing an external warehouse operated by a partner company. First and foremost, the solution offered the benefit of having the future site dedicated completely to spare parts logistics – this would mean that the existing ENGEL plants could once again focus solely on manufacturing. In the place of three mutually independent spare parts warehouses, ENGEL would have a single, central warehouse in Austria with comprehensive and highly efficient processes for its spare parts logistics. At the same time, the reorganization would benefit the existing manufacturing plants by freeing up space that was previously used for spare parts storage and repurposing it for future growth. 4flow provided support in selecting service providers and establishing the external spare parts warehouse. The location of the new, central warehouse facilitates highly efficient processes which enable ENGEL to fill customer orders quickly and flexibly, even with increased future demand.
Flexible, worldwide order fulfillment – even on holidays
4flow supported ENGEL in the service provider selection process, which featured several German and Austrian logistics service providers as candidates. This also included intensive process workshops and onsite inspections of reference locations in both countries. In the end, the choice was made to contract an international logistics company based in Austria – the service provider possessed the appropriate mix of expertise in the spare parts industry and the corresponding processes in the area of value-added services. Furthermore, the partner was willing to commit to rapidly implementing the relocation to the new aftersales site.
The new ENGEL spare parts warehouse will not only provide highly efficient service to customers in Europe, South America, Africa, and the Middle East, but also serve ENGEL’s central spare parts hubs in the US and Thailand for the North American and Asian markets. Fischamend, the location selected for the new spare parts warehouse, is optimally suited to its purpose – it is situated just three kilometers from both the Vienna airport and international CEP service providers. The Bratislava airport is also reachable in just a few minutes by highway, which enables international delivery on Austrian holidays. In this way, ENGEL’s new site allows the company to provide its global customers with up to eight additional delivery days per year.
As an added benefit, the machinery manufacturer’s customers, service organizations, and spare parts hubs can rely upon highly flexible logistics with expanded delivery options, including later cut-off and pickup times. High-priority orders created up until 6:00 p.m. are eligible for same-day shipping. “For our customers, this means shorter stoppages and greater availability of injection molding machinery and production installations,” said Harald Wegerer, vice president of ENGEL’s customer service division. “We are very pleased to have found 4flow as such an outstanding partner for the planning and implementation of our new structures.”
In addition to process optimization, the new warehouse provides ENGEL with a reliable basis for future growth. With 10,000 square meters of floor space, 20,000 pallet slots, 18 loading docks and a total of 2,000 square meters of goods receiving area, the site enables ENGEL to meet the requirements of future growth – the capacities that ENGEL uses in the building are flexible and can be adjusted at any time.
Implementing efficient processes at the new location
Using the strategy paper, ENGEL and 4flow laid the foundations for efficient structures and processes at the new spare parts warehouse. Apart from path optimizations, simplified goods management, and clearly defined communication channels, the site offers optimal inventory transparency. One challenge presented by the project was shifting deliveries from ENGEL’s three Austrian locations over to the unified model at the company’s location at Fischamend. As such, employees from both ENGEL and the new warehousing partner had to be trained, and corresponding processes had to be implemented at the new location. At the same time, it was necessary to relocate existing inventory to the new site quickly and without error – a task which had to be carried out at full capacity in order to keep to the tight relocation schedule of three months.
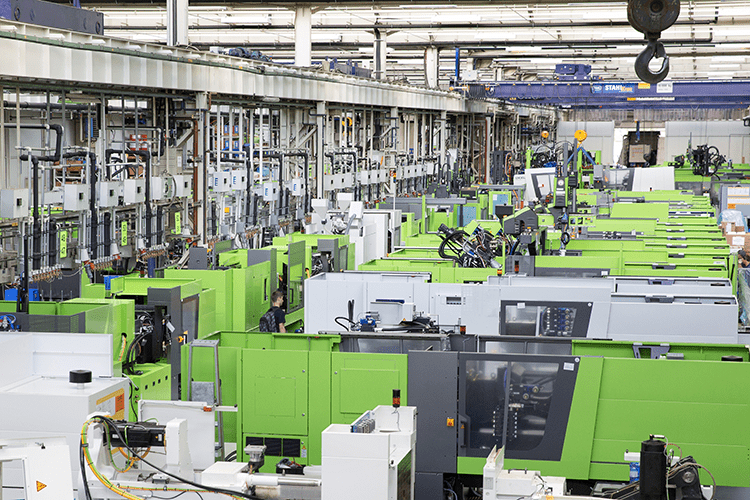
4flow ensured the successful move to the new location and the subsequent go-live by defining necessary processes, creating comprehensive training materials, and assuming responsibility for project management. “The primary challenge of the project was that the constituent structures and processes of the existing ENGEL locations had to be consolidated at the new site in a very narrow time frame,” said Harald Wegerer. “Our collaboration with 4flow and our logistics partner in the context of this demanding project was highly equitable and constructive.” In this regard, the project partners had a robust cooperative approach: In addition to the project team members from ENGEL, 4flow, and the site operator, there were also ENGEL employees from their customer service, legal, purchasing, controlling and accounting, IT, and quality control divisions involved. In collaboration with ENGEL and its logistics service provider, 4flow established systemic interfaces and carried out an audit of the new site before the go-live. “4flow laid the optimal foundation for a smooth handoff to our site operator and the corresponding operational startup” added Mr. Wegerer. “We anticipate that the new warehouse concept’s significant, comprehensive improvements to our delivery performance will give us as a major competitive advantage.”
Contact us
If you’d like to learn more about supply chain management, we’re ready to help.
Related topics
Warehouse planning
4flow supports businesses with the end-to-end planning of well-chosen, cost-optimized warehouses and more efficient warehousing processes.
Digital supply chain
An integrated view of supply chain management, transportation, and intralogistics is the basis of a digital supply chain.
Lean logistics
Innovative lean logistics solutions provided by 4flow reduce costs sustainably and result in standardized internal logistics processes.